고에너지 볼 밀링을 이용한 분산강화된 Fe-TaC 합금분말의 소결거동 및 기계적 특성평가
Sintering Behavior and Mechanical Properties of Dispersed-Reinforced Fe-TaC Composites Produced by High Energy Ball Milling
Article information
Trans Abstract
In this study, a high-melting point element, tantalum carbide (TaC) was added to improve the mechanical properties and the oxidation/corrosion resistance of Fe. The Fe-TaC composites were synthesized by high energy ball milling for the mechanical alloying of the non-equilibrium phase (Fe-Ta) and the homogeneous dispersion of TaC. Fe-TaC composite samples were fabricated using 5, 10, and 20 wt.% TaC. The ductile particles (Fe) got harden and the brittle particles (TaC) were uniformly dispersed, while facilitating short-range diffusion in the ductile matrix by the high energy ball milling method. Spark plasma sintering was performed at a sintering temperature of 850 °C and pressure of 60 MPa. As the TaC contents increased, the sintering exponential (m) increased. A higher ‘m’ value indicates a lower magnitude of shrinkage, by decreasing the lattice and grain boundary (G/B) diffusion path between the pores and particles. The hardness increased from 128.9±10.4 to 444.2±20.6 kg/mm2 as the grain size decreased from 5.13 to 3.99 μm. This enhancement is attributed to the Hall-Petch relationship and dispersion strengthening effect. The mechanical properties of the sintered bodies were studied to evaluate how the different TaC content affect their characteristics. In addition, oxidation resistance increased with increasing TaC contents. It was considered that the local oxidation resistance based on the formation of an oxide layer of TaO and Fe2O3.
1. 서 론
내구성 및 강성이 우수한 Fe 소재는 다양한 산업 분야에서 사용되고 있으나 산업분야의 발전에 따라 기계적 특성 및 내구성이 우수한 제품의 필요성이 대두되고 있다[1,2]. 철 소재의 특성을 향상시키기 위해 다양한 소재가 첨가되고 있으며 최근 전이금속 물질인 티타늄 카바이드(TiC), 탄탈륨 카바이드(TaC)와 같은 카바이드계가 철과 관련된 다양한 분야에서 첨가제로 사용되고 있다[3,4]. 카바 이드 소재는 내화성, 탄성계수, 내마모성 등 우수한 기계적 특성을 가지고 있다[5,6]. 예를 들어, TaC를 Fe에 첨가하면 높은 강도를 얻을 수 있으며, 내열성 및 내부식성이 향상된다[7]. 이러한 특성 때문에 카바이드 소재 첨가에 따른 철 소재의 연구가 활발히 진행되고 있으며, 항공우주, 절삭공구 등 다양한 산업 분야에서 적용되고 있다. 최근에는 카바이드계 분말을 이용한 분산강화 연구가 관심을 모으고 있다[8]. 금속기지에 카바이드계 분말을 물리적으로 혼합 후, 분말야금법을 통하여 열적 안정성과 기계적 강도를 향상시키는 방법에 대한 연구가 이루어지고 있다. 카바이드계 분산강화 기법은 화학적 처리와 물리적 처리 방법이 있다. 화학적 처리 방법은 화학적인 물질을 사용하므로 물질 내부 또는 표면에서 입자 간 화학적 상호작용이 일어나며, 공정비용이 비싸다는 단점이 있다. 카바이드계 분말을 이용한 물리적인 방법 중 본 연구에서 적용한 고에너지 볼 밀링은 입자 간의 충돌로 인한 높은 에너지 상태를 유도하여 입자를 균일하게 분산시키고, 입자크기가 미세화됨에 따라 기계적 특성을 향상시킬 수 있다. 소결 방법으로는 분말 야금법 중 Hot pressing (HP) [9], 상압 소결[10], Hot isostatic pressing (HIP) [11] 등이 사용되었으나 장시간 소결로 인한 입자 성장이 기계적 특성을 감소시키며, 외부 간접 가열 방식 때문에 완전한 밀도에 도달하는 것이 어렵다는 문제점이 있다. 본 연구에서 적용한 방전 플라즈마 소결법(SPS)은 직류 펄스 전류를 소결체 내부에 직접 통전 시키는 방식으로 균일한 물성을 유지하고, 단일공정과 단시간 동안 입자성장을 제어하면서 고밀도의 소결체를 제조할 수 있는 방법이다. 따라서, 본 연구에서는 고에너지 볼 밀링을 이용하여 Fe기지에 TaC 강화입자가 균일하게 분산되도록 혼합분말을 제조하였고, 방전 플라즈마 소결법을 이용하여 고밀도의 Fe-TaC 소결체를 제조하였다. TaC 함량에 따라 제조된 소결체의 소결성, 기계적 특성 및 내산화 특성에 대한 평가를 하였다.
2. 실험방법
초기 원료 분말로는 Fe 분말(Yuelong metal powder Co. Ltd, 순도 99.95%, 5~10 μm)과 TaC 분말(Alfa, LTD, 순도 99.5%, ~4.4 μm)을 사용하였다. 그림 1은 분말의 초기 형상을 관찰하기 위해 주사 전자 현미경 (JSM-7001F, JEOL)을 이용하여 미세조직을 분석한 결과이다.
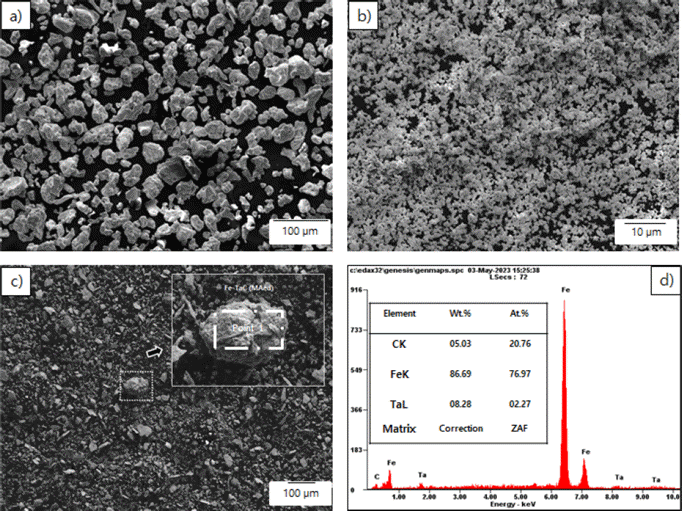
Micromorphology of a) Fe, b) TaC raw powders, c) Fe-10wt.% TaC composite by planetary ball milling and d) point 1 of Fe-10wt.% TaC composite
Fe는 불규칙한 각형이며, TaC는 불규칙한 미립자 형태이다. Fe 분말 100 중량 기준 5, 10, 및 20 중량 퍼센트의 TaC를 첨가하였고, 고에너지 볼 밀링 공정을 수행하였다. 볼은 스테인리스 볼을 사용하였으며, 볼과 분말의 비율은 10:1 중량 비로 강화 스테인리스 용기에 밀봉하여 250 RPM의 속도로 9시간 동안 혼합 분쇄 과정을 거쳤다. 비중 차이가 큰 Fe와 TaC의 균일 혼합을 위해 Process control agent (PCA, 에탄올)을 첨가하였으며, 분말과 PCA의 비율은 100:1 중량비로 설정하였다. 공정이 끝난 후, 진공오븐을 이용하여 24시간동안 건조하였다. 입도분석 장치를 이용한 혼합물 분말의 입도분석 결과 TaC 함량이 증가함에 따라 평균 4.18, 3.86, 및 3.71 μm로 감소되는 것으로 확인되었다. 이는 TaC함량이 증가함에 따라, 취성 분말(TaC)의 파쇄효과가 강화되어 입도 크기가 줄어든 것으로 추정된다.
제조된 분말을 각각 흑연 몰드 (외경: 30 mmØ, 내경: 10 mmØ, 높이: 40 mmT)에 충진하였다. 흑연 펀치로 상하부를 막았으며, 밀봉된 흑연 몰드를 방전 플라즈마 소결 장치 (SPS 9.40 MK-III, Sumitomo Heavy Industries)에 장착 후 약 6 Pa의 진공 상태를 형성하였다. 소결 압력 60 MPa을 인가 후, K-type 열전대를 이용하여 흑연 몰드의 내부 온도를 측정했다. Fe-TaC의 혼합 분말을 승온 속도 60 °C/min으로 500 °C까지 가열한 다음, 1분 동안 등온 후 최종 목표 온도인 850 °C까지 40 °C/min으로 승온하였다. 소결 종료 후 냉각시 600 °C에서 압력을 제거했다. 또한, 소결 공정 중 치밀화 및 강화 거동과 관련된 각 TaC 함량에 따른 소결 거동을 비교하기 위해, 수축 변형률 [식 (1)]을 사용했다[12].
여기서, εs는 수축 변형률, m은 소결 지수, L0은 초기 성형체 (green body)의 길이, ΔL은 거시적 수축 길이 변화, K는 K (T)로 온도에 따른 소결 상수, t는 등온 유지 시간, T는 유지되는 온도이다. 또한 제조된 시편의 밀도는 아르키메데스 방법을 이용하여 밀도를 측정하였다. 소결이 완료된 소결체의 표면 관찰을 위해 Nital solution (1-5% Nitric acid (HNO3) + 99-95% Alcohol (CH3OH))을 이용하여 약 5~10초간 표면을 부식시켰다[13]. 부식법을 통해 표면 부식 후, 주사 전자 현미경을 이용하여 소결체의 미세구조를 분석하였으며, 선형 분석 방법 (ImageJ 프로그램)을 이용하여 평균 결정입도 (grain size)를 측정하였다[14]. 또한, X-ray diffraction (XRD, PIXCEL 1DDETERCTOR, Panalytical)를 통해 상분석을 진행 후, 상분석 결과를 이용하여 Stokes and Wilson’s 식을 이용하여 내부응력 및 격자구조 (lattice parameter)를 측정하였다[15].
여기서 b는 X선 회절 피크는 기계적 보정값의 반가폭(FWHM), bd와 be는 내부응력과 반가폭에 의하여 감소한 크기를 측정한 값이다. K는 Scherrer 상수 (0.9)이며, λ는 X선의 파장 (CuKα, λ = 0.154 nm)을 나타낸다. d와 ε은 결정자 크기 및 내부 응력을 측정한 상수이며, θ는 Bragg 각도를 나타낸다.
기계적 특성 중 경도 특성은 비커스 경도계(HV-100, Mitutoyo)를 이용하여 20 kgf의 하중으로 15초간 유지하였다. 각 시편마다 총 10번 측정 후, 최대 최소를 제외하고 평균값을 택하였으며, 식 (3)를 이용하여 발생된 시편의 압흔 길이를 측정하여 경도를 평가하였다.
여기서, d는 압흔 자국의 대각선 길이이며, K는 압입 의 형상과 관련된 상수 (1.89 x 105), 및 P는 인가 된 하중을 나타낸다. 또한, 소결체의 탄성계수를 분석하기 위하여 나노인덴테이션(HM 2000, Helmut Fischer)을 이용하였다. 실험 방법은 2 kgf 하중을 10초간 인가하고, 식 (4)를 통해 탄성계수를 평가하였다[16].
여기서, Eeff는 시험편과 압입자 사이의 유효탄성계수, β는 인덴터의 형상계수 (1.034), S는 하중 인가 시의 강성, A는 시험편 표면에 압입된 투영접촉면적을 나타낸다. TaC 함량에 따른 Fe-TaC 소결체의 내산화 평가를 위해 ZrO2 용기 안에서 승온속도 10 °C/min으로 900 °C까지 승온했다. 추가적으로 단면에 대한 Scanning electron microscope with energy dispersive X-ray spectroscopy (SEM-EDS)의 정량적 분석을 통해 산화 거동을 분석하였다.
3. 결과 및 고찰
그림 2를 보면, 소결 시간에 따른 소결 온도와 Fe-TaC 소결체의 수축길이 변화 (see 그림 2(a))와 소결 온도에 따른 수축 변형률을 나타내었다 (see 그림 2(b)).
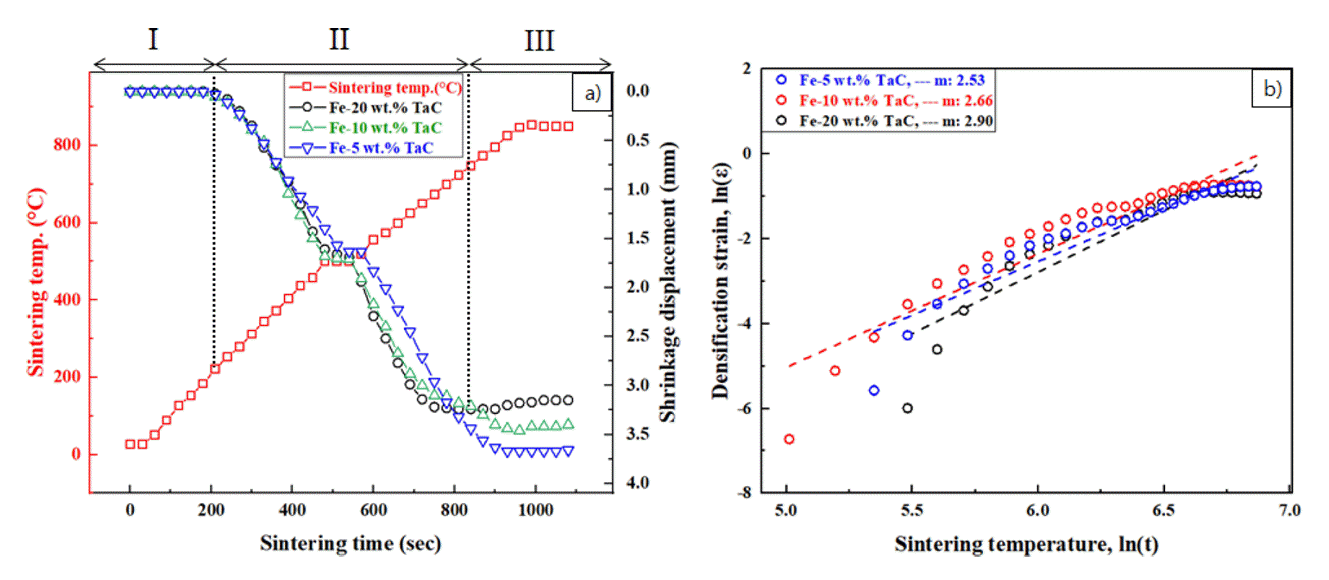
Sintering behavior as a function of TaC contents: (a) sintering temperature and shrinkage displacement and (b) densification strain
수축은 약 200 °C 에서부터 시작되었으며, 850 °C 에서 최종적으로 소결이 종료가 되었다. Fe-TaC 복합체는 수축 변위에 있어 3단계로 나눌 수 있으며, I (32~200 °C), II (200~700 °C), III (700~850 °C)와 같다. I단계에서는 초기 상태에서 분자들간에 약 2~3%의 치밀화만 진행되었다. II단계에서의 치밀화 거동은 목 성장, 기공제거 및 격자 확산과 같은 입자 대 입자 접촉점에서 상호확산 (격자 및 입계)을 촉친한다고 보고 되고 있다[17]. 마지막으로 III단계에서 팽창 원인으로는 Fe (11.8 × 10-6/K), TaC (5.7 × 10-6/K)에 직류펄스전류를 인가함에 따라 발생된 열에 의한 각 소재의 열팽창 차이가 상대적으로 큰 경우에 발생한 것으로 판단된다[18]. Fe-5 wt.% TaC보다 Fe-20 wt.% TaC에서 소결 거동이 느려지고 수축이 덜 되는 이유는 TaC 함량이 증가할수록 젖음성이 감소하여 TaC와 Fe 간의 상호 확산이 억제되어 수축이 덜 이루어진 것으로 판단된다. 결과적으로, 잔류 기공의 제거와 함께 치밀화가 상대적으로 덜 발생한다고 판단된다[19]. 최종 소결체의 상대밀도는 TaC 함량이 증가함에 따라 상대밀도는 95.3, 94.1, 및 92.8%로 감소하는 경향을 보였다. 추가적으로, 그림 2(b)는 소결 시간에 따른 수축 변형률 (εs)을 나타낸 것으로 급격한 수축 거동을 보이는 소결 온도 범위 (약 200~700 °C)에서의 소결 지수 (m)의 변화는 εs에 따라 결정된 것으로 식 (1)을 통해 확인되었다. 식 (1)에 따르면 m값이 낮을수록 거시적 수축의 크기는 커지며, 소결 과정에서의 높은 계면 에너지를 야기시켜, 결과적으로 소결 종료 지점의 온도에 이르러서야 치밀화가 진행되었다고 판단하였다. 이는, 높은 m값을 갖는 Fe-20 wt.% TaC (m = 2.90)의 경우 최종 소결 구간에서의 잔류 기공 제거와 더불어 여전히 완료되지 않은 고상 확산이 지속됨으로써, 높은 활성화 에너지에 따라 낮은 상대 밀도를 가진 것으로 판단하였다[12].
그림 3에서는 Fe와 Fe-TaC의 분말과 소결체의 XRD 상 분석 결과를 나타내었다. XRD 상분석을 통해 총 3가지 주요 사실을 확인할 수 있다. (1) Fe 부피 분율이 감소함에 따라 Fe 회절 피크의 상대적 강도가 약해졌다. (2) C(graphite)와 Fe3C 소량 검출되었다. (3) 분말과 소결체를 비교하였을 때, 격자 상수 차이로 인한 변형률이 존재한다. (1)에 대한 이유는 TaC 함량이 증가함에 따라 상대적으로 Fe가 회절 되는 양이 적기 때문이며, (2)에 대한 이유로는 Gibbs free energy(ΔG)를 이용하였다. Fe와 TaC 복합재료의 제조 과정에서 가능한 반응들과 해당 ΔG 변화를 온도 함수로 나타낼 수 있다[20].
Fe3C에 대해 ΔG 값을 850 °C에서 구해본 결과 ΔG1 = -0.14 kJ/mol이며, 이는 850 °C에서 안정적인 상임을 확인할 수 있다. 그리고 소결 중에 고체 상은 부분적으로 분해된 원자들을 방출하게 된다. 즉, Fe 와 TaC 사이에서 Fe-Ta-C 삼원계를 얻을 수 있다. 이 때, 온도의 영향으로 경계면에서 일부 분해된 Ta 원자들이 존재하고, C 원자들이 빠르게 확산하게 되어 Fe3C가 생성된 것으로 판단된다. 하지만 이때 일부 확산되지 못한 C에 대한 활동도 차이에 의해 Fe입내로 확산되지 못한 free-carbon이 형성된다. 이에 C가 일부 형성된 것으로 판단된다[21]. 또한, 혼합분말이 소결체로 치밀화 되는 과정에서의 Fe의 피크와 격자 상수 차이에 따른 변형률을 비교하였다. 표 1에서 분말이 치밀화되는 과정에서 44.648 °에서 44.531 °로 Fe 피크 이동 현상이 일어났고, 고체 확산에 의해 Ta가 Fe 격자 내로 확산되면서 높은 변형률(0.112에서 0.204)과 함께 격자 상수(2.869에서 2.856 Å)가 감소하였다.
이는 고에너지 볼 밀링 동안 Fe와 TaC입자 사이에 심각한 충돌로 인한 원자 사이에 높은 압축응력에 따른 격자 상수 감소로 판단된다[22]. 따라서, 격자내에 압축 응력을 내재한 고용체 강화(solid solution strengthening)에 의한 경도향상 효과를 나타낼 수 있을 것으로 판단하였다. 그림 4은 소결체의 미세조직 분석 결과를 나타내었다. TaC가 Fe 매트릭스에 분포되어있는 형태로 되어있다.
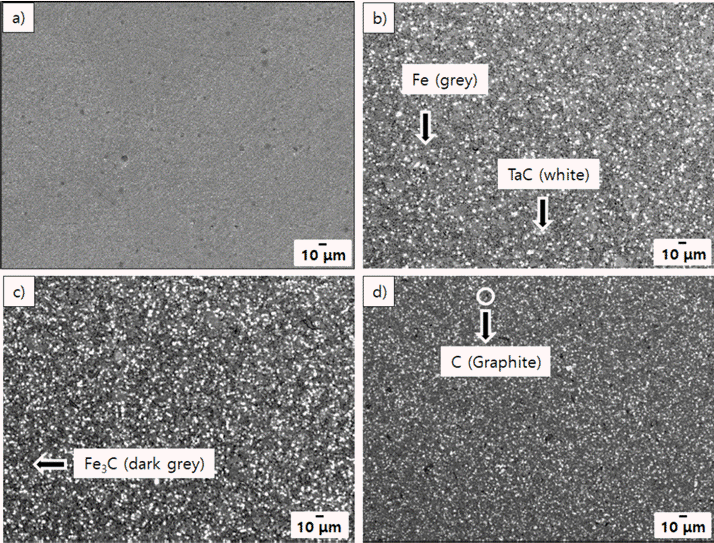
SEM images after sintered at 850°C : (a) Fe, (b) Fe-5 wt.% TaC, (c) Fe-10 wt.% TaC, and (d) Fe-20 wt.% TaC
즉, TaC가 강화재로서 Fe매트릭스에 분포되어 있으며, 고에너지 볼 밀링에 의해 TaC 함량이 증가함에 따라 응집하지 않고 고르게 분산된 것을 확인할 수 있다. 또한 선형분석법으로 각 복합재의 결정립 크기를 측정하였다. 0, 5, 10, 및 20 wt.% TaC 순서대로 5.13, 4.74, 4.53 및 3.99 μm 측정되었으며, 이는 TaC의 높은 계면 에너지로 인해 안정적인 계면이 형성되어 입자 재배열과 입계 확산이 가속화되며, 이로 인해 결정립 미세화가 이루어지고 Fe 결정립 성장이 억제된 것으로 판단된다. 즉, Fe와 TaC계면 사이에의 에너지 차이는 결정립 성장 거동에 영향을 미친 것으로 판단된다[23,24]. 또한 그림 5은 소결체의 확대한 미세조직 분석 결과를 나타내었다. Fe-Ta (MAed)와 Fe 매트릭스에 TaC가 분산되어 있으며, TaC가 코어인 white core grey rim(WCGR)구조를 확인할 수 있다[25].
이는 고에너지 볼 밀링에 의해 만들어진 비평형 상태의 상이며, 기계적 합금화에 기인한 코어-림 구조는 산화 저항력을 향상시키기 위한 역할을 하며, 산화 반응에 대한 활성화 에너지 분포에 따른 감소와 결정성장을 억제할 수 있다고 보고된다[25,26]. 그림 6은 각 함량에 따른 기계적 특성 평가 결과를 나타내었고, 표 2에서는 소결체의 평균 경도, 탄성계수, 결정립 크기 및 상대밀도를 나타내었다. TaC 함량이 증가함에 따라 경도 값은 증가함을 보여준다. TaC에 의한 분산강화 효과와 결정립 성장 억제에 따른 Hall-petch 관계식에 기인한 결정립계 강화 효과가 상호작용하여 Fe-20 wt.% TaC에서 가장 높은 경도 값(444.2±20.6 kg/mm2)을 나타냈다. 일반적으로, 탄성계수 측정 결과 보통 경도가 높은 재료는 탄성계수도 높아 강성이 크다고 볼 수 있다. 하지만 이러한 상관관계가 모든 재료에 대해 보편적으로 적용되는 것은 아니며, 결합 유형 및 미세구조와 같은 여러 요인에 의해 영향을 받는다[27]. 예를 들어, TaC 입내로 균열의 선단이 흡수되면서 전파하려는 거동에 따른 낮은 계면 에너지에 의하여 탄성계수는 상대적으로 감소할 수 있다고 판단하였다[28-29]. 그림 7은 Fe, Fe-(5, 10, 및 20) wt.% TaC 소결체를 ZrO2 용기에서 900 °C까지 노출 시킨 후의 XRD를 보여준다.

a) Mechanical property of Fe(pure), Fe-5, 10, 20 wt.% TaC sinterd-bodies, b) Load P according to depth for elastic modulus
Fe에서는 Fe2O3와 Fe3O4의 피크가 모두 확인되며, TaC함량이 증가할수록 Fe2O3의 피크만 확인된다. 이는 반응성이 높은 Fe3O4구조 안에는 Fe2+이온과 Fe3+이온이 혼재되어 있으며, 고온 상태에서는 Fe3+이온이 Fe2+이온으로 산화된다. 이러한 반응에 의해 Fe3O4가 Fe2O3으로 결정체가 생성된 걸로 판단이 된다. 900 °C에서 생성 가능한 반응들과 해당 Gibbs free energy (ΔG)의 값을 나타낼 수 있다[30].
Fe2O3, Fe3O4에 대해 ΔG 값을 구해본 결과, ΔG2 = - 260.4 kJ/mol, ΔG3 = -742.5 kJ/mol이며, 이는 900 °C에서 안정적인 상임을 확인할 수 있다. TaO상은 TaC가 600 °C에서 900 °C 사이에서 생성되며, TaC가 800 °C 이상에서 산화시키면 TaO상은 아래와 같은 반응을 나타나게 된다[31].
하지만 본 연구에서는 낮은 온도에 의해 Ta2O3상이 아닌 TaO상이 Fe-10, 20 wt.% TaC에서 확인되었다. 또한 TaO와 Fe2O3가 산화막을 형성함에 따라 높은 내산화를 가지며 이러한 특성으로 인해 TaC함량이 증가함에 따라 내산화 특성이 우수해지는 것으로 판단된다[32]. 그림 8은 Fe, Fe-(5, 10, 및 20) wt.% TaC 소결체를 ZrO2 용기에서 900 °C까지 노출 시킨 후의 미세조직을 보여준다.

Elements line profile from oxidation layer to matrix: a) Fe, b) 5 wt.% TaC, c) 10 wt.% TaC, d) 20 wt.% TaC and e) quantitative data of oxygen
TaO가 없이 Fe3O4와 Fe2O3만 공존하고 있는 Fe 소결체는 산소 (O) 피크가 안쪽까지 확인이 되었다 (그림 8(a)). 하지만 TaC함량이 증가함에 따라 Fe2O3와 TaO가 산화막을 형성에 따라 국부적인 내산화성에 기인한 산소 피크의 급격한 감소로 판단된다 (그림 8(b, c, d)). 그림 8(e)는 각 소결체에 대한 산소 피크를 정량적인 데이터 그래프로 나타내었다. Fe 소결체는 T.O.L(Thickness of oxidation layer)이 239.16으로 산화가 내부까지 일어난 것을 확인할 수 있으며, TaC함량이 증가함에 따라 T.O.L과 I.A(Integration of area)값은 줄어들었으며, 이는 내산화성 증가에 중요한 역할을 했다고 판단된다.
4. 결 론
TaC 분말을 사용하여 분산강화 및 Fe 분말과 균일 혼합 공정을 위해 고에너지 볼 밀링 공정을 수행하였다. TaC함량에 따른 혼합 분말을 방전플라즈마 소결법을 이용하여 단 시간 내에 치밀한 Fe-5, 10 및 20 wt.% TaC 조성의 소결체를 제조하였고, 다음과 같은 결론을 얻었다.
(1) Fe-TaC복합체의 소결 거동은 소결지수 (m)과 열팽창 계수에 따라 결정되었다. TaC함량이 증가할수록 m 값은 커지며, 거시적 수축의 크기는 작아졌다. 또한, 20 wt.% TaC에서 상대적으로 낮은 상대밀도를 나타내었는데, 이는 치밀화가 소결 종료 지점의 온도에 이르러서야 진행된 것으로 판단된다.
(2) 기계적 특성은 탄화물의 결정립 사이즈 및 내부 격자 변형 및 분산 강화에 따라 강화 거동이 결정되었으며, 20 wt.% TaC에서 가장 높은 경도 (444.2±20.6 kg/mm2)를 보였다. 반면에 탄성계수는 Fe/TaC의 계면 상태에 따른 계면 에너지 차이에 의해 결정되었으며, 20 wt.% TaC에서 가장 낮은 탄성계수(155.9±3.4 GPa)를 보였다.
(3) 내산화성 특성은 XRD, SEM-EDS의 정량적인 데이터를 통해 분석되었다. TaC함량이 증가함에 따라 I.A, TOL값이 작아지며, Fe-20 wt.% TaC에서 가장 낮은 I.A(764.59), T.O.L(~42.34 μm)를 보였다. 따라서 Fe-20 wt.% TaC가 높은 경도 및 내산화 특성이 우수한 특성을 가지는 것으로 분석되었다.
Acknowledgements
본 논문은 한국생산기술연구원 기관주요사업 ‘‘하드페이싱용 스텔라이트 합금소재 연속주조/분말재조/선재가공 양산급 소재기술 및 장기수명을 위한 경사기능형 용접코팅 공정기술개발 (KITECH EO-23-0008)’’의 지원으로 수행한 연구입니다.