IN 625 초내열합금의 응고거동 및 상변태 온도 분석
Study on Solidification and Phase Transformation Behaviors in Ni-based Superalloy IN625
Article information
Trans Abstract
The solidification and phase transformation behaviors of IN625 with low C and Fe were investigated through directional solidification and quenching experiments. The primary and secondary dendrite arm spacing decreased exponentially as the solidification rate increased, demonstrating good agreement with theoretical equations. The MC carbide formed at a constant temperature gradient regardless of the solidification rate. It is reasonable to assume that the Laves phase solidified in the final stage of solidification, as it was found at the bottom of the mushy zone. The morphologies and sizes of the MC carbide and the Laves phase were closely related to the solidification rate. Increasing the solidification rate at a constant thermal gradient resulted in the development of the MC carbide from blocky to Chinese script, and eventually spotty shapes, along with decreasing size. As a result of this research, it is believed that the weldability of the alloy could be improved at the expense of mechanical properties, especially with low C and Fe contents and a relatively high solidification rate, which are able to generate the finely distributed MC and Laves phase.
1. 서 론
IN625합금은 고용강화형 Ni기 초내열 합금으로 극저온에서 약 800°C 까지의 고온 환경에서 우수한 강도와 부식 및 산화 저항성을 갖고 있다. 또한 용접성 및 성형성이 뛰어나 항공, 화학, 해양 산업에 널리 사용되고 있으며 보수 용접 및 적층 제조공정으로 적용성도 유리한 합금이다[1-3]. 이 합금은 Ni 기지에 주요합금원소로 Cr, Mo, Nb을 함유하며 MC, Laves, M23C6, M6C, γ², δ상 등 다양한 탄화물과 2차상이 형성될 수 있으며[4-6], 가스터빈 및 고온 구조용 부품에 다양하게 적용되고 있다. 대형 가스터빈이나 복잡한 고온 구조재료 및 대형 부품에서 강도와 용접성이 뛰어난 주조재가 요구됨에 따라[7] Nb이 첨가된 625, IN718, IN909, Rene 220C 등과 같은 고용강화형 또는 석출경화형 합금이 개발되었다. 이러한 합금들은 뛰어난 용접성에도 불구하고 주조 또는 용접 도중 응고의 마지막 단계에서 HCP 구조를 갖는 Laves 상의 정출로 인해 기계적 특성 및 용접성이 저하되는 것으로 알려져 있다[8]. 이 합금들에 대한 연구는 주조, 단조, 열처리, 용접, 클래딩, 적층 제조 등 제조공정과 그에 따른 기계적 특성을 개선하기 위한 다양한 연구들이[6-9,11-14] 진행되었으나 제조공정에 있어 가장 기본이 되는 응고과정을 수반함에도 불구하고 응고거동에 관한 연구[10]는 상대적으로 많지 않다.
합금의 응고거동에 관한 연구는 응고시 열전달 관련 공정변수를 최적화하는 과정을 수반하고, 응고계면에서의 미세조직 제어를 통해 합금성분의 편석 및 주조결함을 최소화할 수 있을 뿐 아니라 최종적으로 열간 성형 또는 열처리와 같은 후공정을 통해 기계적 특성을 향상시키는데 그 목적이 있으며 부수적으로 제조기간과 비용이 절감되는 이점이 있다. 따라서 본 연구에서는 IN625 합금의 응고거동을 일방향응고 및 급냉(directional solidification and quenching: DSQ)에 의해 응고 도중 형성되는 미세조직을 통해 분석하였다. 공정변수에 의한 오차를 최소화하기 위하여 일정한 온도구배 조건에서 응고속도 변화에 따른 고상/액상 응고계면에서 미세조직 변화를 관찰하였다. 또한 실제 응고 공정 중에서 발생하는 상 형성 과정을 열역학 계산결과와 비교 분석하였고, 공정변수에 따른 미세조직 변화를 이론적으로 해석하여 응고변수가 계면 미세조직 형성에 미치는 영향과 원인을 규명하고자 하였다.
2. 실험방법
본 연구에서는 용접성을 고려하여 IN625합금 조성 범위에서 C와 Fe 함량을 최소로 한 합금을 표 1과 같이 선택하였다. IN625합금은 규격[1,2]에서 조성 범위를 나타내었고, 본 연구에서 사용된 625합금의 조성은 XRF(X-ray fluorescence, Shimadzu/KRF-1800)분석한 결과를 나타내었다.
표 1의 조성으로 상예측 소프트웨어 ThermoCalc(Vesion 3.1, DB TTNi7)를 이용하여 응고 및 냉각 과정에서 나타날 수 있는 상과 상변태 온도를 예측하였으며 Scheil 식을 이용한 계산을 수행하였다. 시차열분석기(Differential Scanning Calorimetry: DSC, NETZSCH model: DSC 404C Pegasus) 이용하여 고상선, 액상선 및 각상의 석출온도 등을 10K/minute의 승온 및 냉각속도에서 측정하여 ThermoCalc로 예측한 응고 거동과 상변태 온도와 비교 분석하였다.
일방향응고 및 급냉법(DSQ)로 이와 같이 측정한 소재의 열적 특성을 미세조직을 통해 확인하였다. 개량형 Bridgman 장치 이용하여[15.16] 일방향 응고중 급냉에 의해 고체/액체 계면을 보존하여 625합금의 응고 중 조직변화를 관찰하였다. 일방향응고는 모합금을 방전가공에 의해 4.7Ø×100 μm로 채취한 후 표면의 재용해 영역(recast layer)과 산화층(oxide layer)을 제거한 다음 알루미나 튜브(내경: 5 mm, 길이: 700 mm)에 장입한 후 일방향 응고 시험 장비에 고정시켰다. IN625 시편 장입 후 알루미나 튜브는 진공 및 불활성 분위기에서 1600°C까지 가열한 다음 30분 동안 유지하였으며, 가열로를 일정한 속도로 위쪽 방향으로 50 mm 이동시킨 다음 알루미나튜브를 순간적으로 하부에 위치한 수조에 급냉시켜 응고계면을 상온까지 유지시켰다. 일방향 응고는 온도구배 G=12.7 K/mm에서 각각 0.5, 1, 5, 10, 25, 50, 100 μm/s의 속도로 진행하였다.
응고계면의 미세조직은 각 시편을 횡방향 및 종방향으로 절단 후 연마하여 Kalling’s II 용액 (3 g Cucl2, 30 ml HCl, 70 mL Ethanol)으로 부식시켜 광학현미경(OM, NIKON / ECLIPSE MA200)과 주사전자현미경 (SEM, JEOL/JSM-6510)에서 관찰하였으며, 전계방사형 주사현미경 (FE-SEM, TESCAN / MIRA I LMH)을 이용하여 수지상 사이의 편석거동 및 응고된 상의 성분을 분석하였다.
3. 실험 결과
3.1 상평형 계산
본 연구에서 사용한 소재인 표 1 조성의 IN625합금에 대해 ThermoCalc 계산을 통해 각 온도에서 평형상의 형성과 분율을 예측하였으며 그 결과는 그림 1과 같다. 그림 1(a)와 같이 625합금은 각 온도에서 다양한 상들이 나타난다. 응고 거동을 보면 γ 기지상은 1364°C에서 응고하기 시작하여 1260°C에서 응고가 완료되며, MC 탄화물은 1260°C에서 형성되어 900°C 까지 구간에 존재한다. 실제 합금의 응고시 액상에서의 확산은 무한대이고 고상에서의 확산은 일어나지 않는다고 가정한 Scheil식을 적용하면 그림 1(b)와 같은 응고거동을 예측할 수 있다. 즉, 평형거동과 마찬가지로 1364°C에서 γ 기지상의 응고가 시작되지만 용질원소의 잔여 액상중의 편석으로 인하여 1147°C에서 Laves상이 나타나기 시작하고, 1134°C에서 δ상이, 1113°C에서 η상이 형성되기 시작하여 1103°C에서 응고가 종료되는 것으로 나타난다. 이는 평형응고(그림 1(a))와는 달리 수지상사이에서 편석을 고려하였기 때문에 Laves상, δ상, η상이 형성되는 것으로 나타났다. 3.3절에 언급하는 실제 응고조직인 일방향응고 조직에서는 δ와 η상은 관찰되지 않았다. Scheil계산에서는 평형상태도와 달리 고상에서의 확산이 없다고 가정하였고, 실제응고에서는 Scheil식과 달리 고상의 확산이 일어나기 때문에 평형상태 Scheil식, 실제응고에서 상의 존재 및 분율에서 차이를 보여주는 것으로 판단된다. Scheil 계산에 의하면 그림 1(b)와 같이 약 261°C의 상당히 긴 응고구간을 갖는다.
3.2 열분석
DSC 분석을 통해 본 연구에서 사용된 IN625합금의 용융 및 응고하는 동안 상변태 거동을 확인하였으며, 그 결과는 그림 2와 같다. 그림 2(a)의 가열곡선에서 3개의 피크가 관찰되었으며 고상선 온도(Ts)는 1338°C 및 액상선 온도(TL)는 1383°C로 나타났다. 냉각곡선[그림 2(b)]에서 γ 기지가 1355°C에서 형성되기 시작하여 1248°C에서 응고가 종료되는 것으로 나타났으나, MC 탄화물과 Laves상의 형성은 명확히 구분할 수 없었다. 이 결과에서 액상선과 고상선의 차이(TL-TS)는 45°C, 응고구간(TL-TE)은 107°C인 것으로 확인되었다. 이들 각 온도는 앞에서 언급한 바와 같이 10 K/minute의 승온 및 냉각속도에서 측정한 값으로 평형응고 및 Scheil식으로 계산한 ThermoCalc 예측과는 다소의 차이를 보인다.
3.3 일방향응고 거동
그림 3은 온도구배를 일정하게 유지시킨 후 응고속도의 변화시켜 얻은 응고계면의 미세조직이다. 응고속도 0.5 μm/s 에서는 셀형 계면이 나타난다. 반면, 1 μm/s 이상의 속도에서는 1차와 2차 수지상이 형성된 전형적인 수지상 조직이 형성된다. 또한 응고속도의 증가에 따라 알려진 바[21]와 같이 수지상 간격 좁아짐을 알 수 있다. 이는 상대적으로 빠른 냉각속도에서는 수지상 팁에서 배출된 용질원소의 농도구배로 인한 조성적 과냉과 높은 온도구배 조건에서 하부로 열전달에 의한 냉각에 따라 1차 수지상가지 사이에서 2차 수지상가지가 형성되며, 응고속도가 빠름에 따라 수지상의 가지가 빨리 형성됨에 따라 1차 및 2차 수지상의 간격(PDAS, SDAS)이 미세해진 것으로 판단된다[21].
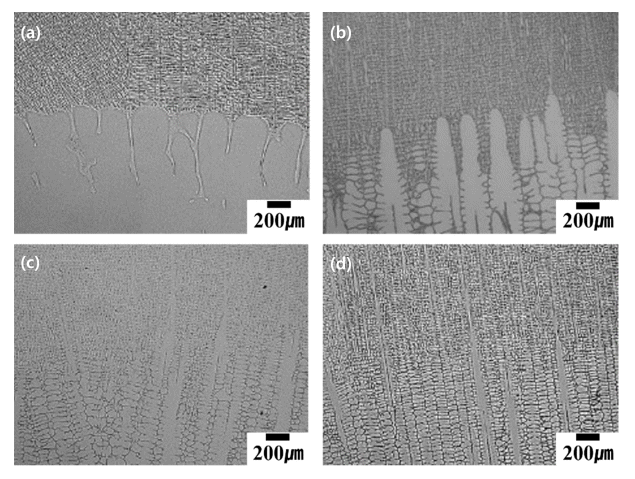
The preserved solid/liquid interfaces on directional solidification at solidification rates of (a) 0.5, (b) 5, (c) 25, (d) 50 µm/s
그림 4는 그림 3에서 관찰한 수지상의 팁에서 약 15 mm 아래의 횡단면 조직들이다. 그림 4(a)의 경우, 1차 가지 사이가 구분되지 않으며 이것은 셀 및 셀>수지상 천이영역에서 1차 가지 사이의 합금원소 편석이 심하지 않기 때문인 것으로 판단된다. 그림 3의 응고계면 미세조직과 마찬가지로 5 μm/s 이상의 속도에서는 잘 발달된 2차 수지상이 관찰되고 응고속도가 증가에 따라 1차 및 2차 수지상들이 미세해지고 1차 수지상의 간격(PDAS)이 감소하는 것을 알 수 있다.

Cross sectional micrographs at 15mm below the solid/liquid interface tip at solidification rates of (a) 0.5, (b) 5, (c) 25, and (d) 50 µm/s
그림 5는 수지상 사이에 나타나는 상들의 응고속도에 따른 형태 변화를 관찰한 것이다. 먼저, SEM-EDS 분석결과, 그림 5(a)~(d)에 관찰된 입자들은 Ni, Cr, Nb, Mo 등이 많이 함유된 조성으로 Laves상임을 확인하였으며, 그림 5 (e)~(h)에서 관찰된 입자들은 대부분 Nb, Ti이 많이 함유된 MC 탄화물인 것을 확인하였다. Laves 상은 초정 γ 형성 이후 잔류액상에서 응고 마지막 단계에서 형성되는 초정 γ+Laves 공정상으로써 5 μm/s 에서와 같은 저속에서는 다소 불규칙하고 조대한 Lamella 형태로 관찰이 되었고, 50 μm/s 이상에서는 응고속도가 증가할수록 층간 간격이 균일한 Lamella 형태로 바뀌는 것으로 확인하였다. MC 탄화물은 응고속도의 증가에 따라 블록형태(이하 blocky 로 표기)에서 늘어나거나 복잡한 형상(Chinese script: 이하 script로 표기) 및 점상(이하 spotty)으로 바뀜과 동시에 크기는 줄어드는 것을 확인할 수 있다. 그림 5에서 (e)는 Blocky 형상, (f)는 Script 형상, (g) 및 (h)는 Spotty 형상을 나타낸다. 일반적으로 MC탄화물은 고체/액체 공존구간(mushy zone)에서 정출하므로 수지상 사이의 간격과 응고 변수에 따라 그 크기와 형상이 영향을 받는 것으로 알려져 있으며[17,22], 이들은 응고변수인 온도구배(G)와 응고속도(R)의 비율인 G/R에 따라 결정되며 G/R 비율이 감소 할수록 script, spotty 모양으로 바뀌게 된다.[17,22] Laves 상은 MC 탄화물에 비해 수지상 팁에서 상당히 떨어진 아래 부분에서 관찰이 되었다. 이는 그림 1 (b)의 Scheil계산에서 예측된 바와 같이 γ 기지상이 형성된 후 잔여 액체에서 형성된 것과 일치하며 Laves상이 MC보다 낮은 온도에서 형성된 것을 의미한다. Laves 상은 층상형태로 나타났으며 응고속도가 증가함에 따라 층간 간격이 넓고 조대한 형태에서 간격이 좁은 형태로 변화되는 것으로 관찰되었다. 그러나 ThermoCalc 계산으로 예측된 δ와 η상들은 관찰되지 않았다. 수지상 하부에서 Laves 상 이외의 다른 상들은 관찰되지 않은 사실로 유추해 볼 때 Laves 상은 γ+Laves 반응으로 형성된 공정조직형태이며, 잔류 액상에서 이 상들이 형성되면서 응고가 종료된 것으로 가정할 수 있다[18].
4. 고 찰
4.1 응고 거동
그림 2에 나타낸 DSC 분석결과, 그림 2(b)의 냉각곡선에서 1355°C γ 기지상 형성 이후 뚜렷한 피크는 나타나지 않음에 따라 1248°C에서 응고가 종료된다고 판단하였다. IN625 상용합금의 경우 MC 탄화물인 NbC는 약 1250°C 부근에서 정출되며, Laves 공정반응은 약 1150°C에서 발생한다[9]. 평형상 계산에서 MC 탄화물은 예측되지 않았고, DSC결과에서 Laves 상과 MC 탄화물의 피크가 발견되지 않았으나 일방향응고 후 조직에서는 관찰되고 있다. 이것은 본 연구에 사용된 합금성분에서 MC 탄화물을 구성하는 주요 원소인 C와 Laves 상의 형성에 큰 영향을 미치는[19] Fe의 함량이 상용합금에 비해 매우 낮아 그 함량이 상대적으로 적음에 따라 응고(정출)시 발열량이 적고, 일방향 응고 (DS)에 비해 상대적으로 빠른 냉각속도에서 DSC분석이 진행됨에 기인한 것으로 사료된다.
이는 MC 탄화물 및 Laves 상은 낮은 함량의 C와 Fe에 의해 상대적으로 액상의 양이 적고 가장 용질원자의 농도가 짙은 응고 후반부(고체/액체 공존구간의 하부; mushy zone 하부)에 형성됨에 따라 γ 기지상의 응고에 따른 발열과 중첩됨에 기인되며, 이 상들이 고체/액체 공존구간에서 형성되는 것을 그림 6에 각 부분의 미세조직과 함께 도식적으로 나타냈다. 그림 6에서 응고속도와 무관하게 수지상 사이의 액체부분 전체에 심지어 1차 수지상 상부 부근까지도 미세한 MC 탄화물이 발견되지만 이들은 급냉(quenching) 중 액체의 온도가 떨어짐에 의한 것으로 실제 고체/액체 공존구간에서 발생하는 현상은 아니다. 반면 응고하는 동안 정출 된 초정 MC 탄화물은 응고의 후반부(수지상 하부)에 나타나고, 고체/액체 공존구간 내 MC 탄화물과 가까운 영역에서 Laves 상(공정조직 형태)이 함께 형성됨을 알 수 있다.

Schemetic drawing of dendrites and interdendritic region and microstructures at various positions on directional solidification of Alloy 625 : (a) Quenched MC carbide in liquid region between dendrites, (b) primary MC carbide at interdendritic region, (c) schemtic drawing of mush zone, and MC carbide and Laves phase near bottom of interdendritic at solidification rates of (d) 10 µm/s, (e) 50 µm/s
ThermoClac 계산에서도 예측되었지만 모식도에 그려진 상 이외에도 γ’, γ”, Ni2(Cr,Mo), d상 등이 석출될 수 있지만[20], 본 연구에서 수행한 일방향 응고실험의 경우 성장속도는 최대 100 μm/s이고 50 mm 성장 후 수냉하는 조건이기 때문에 위의 다양한 상들의 분율이 낮고 석출온도구간을 지나는 시간이 상대적으로 짧아 관찰되지 않은 것으로 판단된다. 또한 IN625 합금 시스템에서 C/Nb의 비율에 따라 크게 3가지의 응고형태를 가질 수 있으나[19], 본 연구에서 사용된 합금의 조성은 매우 낮은 C의 함량을 가지므로 MC가 나타나지 않는 L→ L + γ→ L + γ + Laves→ γ + Laves 형태를 고려할 수 있으나, 실험결과 L → L + γ→ L + γ+MC→ γ+MC + Laves로 응고하는 것으로 확인되었다. 이는 C의 함량이 낮지만 응고 마지막 단계에서 잔류 액체에 농축된 C가 MC 탄화물[32,33] 형성에 기여한 것으로 판단된다.
4.2 일방향응고 조건과 상형성 관계
합금의 편석거동, 기계적 성질, 열처리 시간 등을 정량화 할 수 있는 척도인 PDAS 및 SDAS는 일반적으로 아래식의 거동을 따른다[21].
여기서 K1, K2는 재료상수 값이고 G는 온도구배, V 응고속도 이다, 온도구배(G)는 본 실험인 일방향응고에서 일정하게 부여했기 때문에 PDAS 및 SDAS를 결정하는 주요 변수는 응고속도(V)에 의해 변한다. 따라서 그림 3 및 그림 4와 같이 응고속도가 증가함에 따라서 PDAS 및 SDAS는 감소하는 경향을 나타내고 그림 7에서 확인할 수 있다.
PDAS 및 SDAS 뿐 아니라 탄화물과 공정상 또한 응고 속도가 증가함에 따라 그림 5와 같이 형상이 바뀌게 되며 Liu의 연구[22]와 같이 탄화물의 형상은 응고속도 증가에 따라 Blocky에서 Script 및 Spotty 형태로 바뀌게 된다. 응고의 마지막 단계에서 형성되는 공정상은 확산 지배적 과정(diffusion controlled process)으로[18] 10 μm/s 이하의 느린 응고속도에서는 비교적 확산할 수 있는 시간적 여유가 충분하기 때문에 Laves 공정조직의 간격이 상대적으로 크게 나타나고, 25 μm/s 이상의 속도에서는 응고속도가 증가할수록 공정조직의 간격은 미세하게 감소하는 경향이 보인다[그림 5(a)-(d)].
특히, 응고속도가 매우 느린 0.5~1 μm/s에서는 정출물들이 거의 발견되지 않았는데, 이는 느린 속도의 조대 셀형 응고계면에서 거시편석이 일어나게 되며 이에 따라 일방향 응고 시편의 초기 및 중기 셀형 계면에서는 MC 탄화물 또는 공정상이 형성될 수 있는 액상조성에 도달하지 못했기 때문인 것으로 판단된다[18]. 이와 반대로 수지상이 잘 발달한 경우에는 평면 또는 셀형 계면에 비해 배출된 용질 원자들이 1차 수지상 사이에서 상당히 큰 농도구배에 의해 2차 가지가 발달하게 되며 이로 인해 이 영역에서 MC 탄화물이나 공정조직의 형성이 가능한 조성에 쉽게 도달하게 된다.
4.3 응고계면 온도 변화
일방향응고 조건에 따라 수지상의 간격이 변함과 함께 고체/액체 공존구간에서 형성되는 각 상들의형상과 크기가 변한다. 응고조건에 따라 즉, 공정변수에 따라 과냉도가 변하기 때문이고 응고계면의 과냉도를 측정하는 것은 합금의 응고거동을 이해하는데 매우 중요하다. 그림 8의 (a)는 ThermoCalc를 이용하여 본 연구에서 사용 된 합금의 조성을 적용하여 Nb의 함량의 변화에 대한 가상 2원계 평형상 태도이다. 실제 미세조직에서 나타난 경향을 이론적으로 정립된 관계식으로 증명하기 위해 응고계면의 과냉도를 계산하여 응고속도에 따른 계면온도를 구한 것은 그림 8 (b)와 같다.

(a)Pseudo binary phase diagram (a), and (b) calculated solid/liquid interface temperature with solidification velocity.
응고속도 변화에 따른 평면, 셀, 수지상 계면의 온도는 다음 식(3)을 이용하여 계산하였다[23].
여기서 Ti(γ)는 수지상 팁의 온도를 나타내며 P는 용질원자의 Péclet 수이며 P=VR/2D로 표현 된다. Iv(P)는 Ivantsov 함수[24,25]로 Needle형 수지상에 대해 Iv(P) = Pexp(P)E1(P)로 표현되고, E1(P)는 적분지수함수로 ∫[exp(- z)/z]dz이며 z는 거리를 나타낸다. R은 셀 또는 수지상 팁의 곡률반경이고, 상수 A = [1-(1-k)Iυ(P)] -1로 표현된다. 본 식에서 부분은 수지상 사이에서 수지상 팁까지 발생하는 용질원자에 의한 과냉도, 수지상 계면에서 액상으로 배출되는 용질원자의 과냉도, 은 수지상 팁의 계면에너지에 의한 과냉도로 표현된다. 이 식의 계산에 물리상수 값은 기존에 알려진 문헌과[26-28] 본 연구에서 분석한 결과를 적용하였다.
식 (4)로 평면형 계면에서 셀형 계면으로 천이하는 임계 속도를 구할 수 있으며[29], (G/V)C>ΔT0/D의 조건을 만족하면 평면형 계면이 안정하게 유지된다는 의미를 가지고 있다. 또한, 식 (5)로 셀형 계면에서 수지상 계면으로 천이하는 임계속도를 얻을 수 있다[30]. 평면형 계면에서 셀형 계면으로 천이하는 임계속도 VP→C = 0.47 μm/s로 계산되었고, 셀형 계면에서 수지상 계면으로 천이하는 임계속도 VC →D = 1.32 μm/s로 계산되었으며, 이는 그림 4에서 관찰된 고상/액상 계면의 변화와 상당히 유사한 경향을 갖는다.
그림 9(a)에 측정된 고체/액체공존구간(mushy zone) 길이를 수지상으로 도식화하여 나타내고, 조직사진으로부터 측정된 초정 MC 탄화물 및 Laves상까지의 거리를 표시하였다. 각 상이 나타나는 거리를 온도로 환산하여 그림 9(b)에 나타냈다. 그림 9(a) 및 (b)에서 MC 탄화물 및 Laves 상의 온도 및 위치는 상대적으로 과냉도의 영향을 적게 받는 Laves 상[31]을 기준으로 수지상 팁, MC 탄화물 형성 위치를 도식적으로 나타낸 것이다. 응고속도가 증가함에 따라 고상/액상 공존구역은 증가하는 경향을 보이지만, 응고계면 액상에서 정출되는 초정 MC 탄화물의 경우 응고속도에 관계없이 대부분 응고의 후반부에 나타나는 것을 확인하였다. 그림 8의 (b)의 수지상 팁의 온도와 마찬가지로 고상/액상 공존구역은 약 25 μm/s 이상의 응고속도에서 거의 일정한 거동을 보이며, 실제 미세조직과 계산치가 상당 부분 일치하는 것을 확인하였다.
5. 결 론
IN625합금의 응고공정과 상변태온도를 ThermoCalc 계산과 DSC 를 이용하여 분석하였고, 이를 실제 응고상변태를 일방향 응고 계면에서 비교하였다. 상형형온도계산, DSC 분석, 일방향응고실험을 통하여 상변태온도를 계산, 측정, 실제응고 결과로 부터 평형상태와 비평형 응고의 차이에 따른 각상의 형성온도 차이를 비교 분석하였다.
일방향 응고된 미세조직을 통하여 분석된 625 합금의 응고 거동은 다음과 같이 나타났다.
L → L + γ → L + γ + MC → L + γ + MC + Laves → γ + MC + Laves
고상/액상 공존구역의 길이 및 수지상 팁의 온도는 응고속도가 증가함에 따라 증가하는 경향을 보였으며 약 25 μm/s 이후의 속도에서는 큰 변화를 보이지 않았다. 응고속도가 증가함에 따라 Laves 상은 조대한 셀에서 간격이 좁은 층상(Lamellar)형태로 진화하였으며, MC 탄화물은 Blocky → Scrip → Spotty 모양으로 바뀌었다. MC 탄화물은 응고속도와는 무관하게 거의 일정한 온도에서 형성되었다.
응고속도의 증가에 따라 Laves, MC의 크기가 미세해짐은 상대적으로 빠른 응고속도의 용접공정에서 이들 상이 미세하게 분산됨을 의미하고, 이는 C와 Fe를 낮춘 625합금의 용접성 개선에 도움이 될 것으로 판단된다.
Acknowledgements
본 연구는 2022년도 산업통상자원부의 재원으로 한국에너지기술평가원(KETEP)의 지원을 받아 수행한 연구과제(No. 20211110100010 & 20193310100090)입니다.