전로 제강 공정에서 초음속 산소 랜스가 2차 연소에 미치는 영향 - 전로 모사 가스 반응로 실험 및 해석
Effect of Supersonic Oxygen Lance on Post-Combustion in Converter Steelmaking Process – Experiment and Analysis with Converter Simulator
Article information
Trans Abstract
Employing post-combustion technology in the converter, using the sensible heat of the hot metal and the oxidation reaction heat as a heat source, is known to compensate for insufficient heat in the converter process. However, most studies on post-combustion have been conducted using subsonic nozzles, whereas actual converter processes use supersonic nozzles. Therefore, research on the combustion behavior of supersonic jets is needed. In this study, experiments and analyses were conducted using a converter simulator and a supersonic nozzle to investigate the effect of nozzle height on the post-combustion behavior. The reaction was set to complete combustion, with an O2gas flow rate of 150 L/min blown through the upper lance and a CO gas flow rate of 300 L/min blown at the bottom of the simulator to represent the surface of the molten metal. The combustion reaction of CO gas was calculated to be rate-controlled by reactant mixing. The nozzle heights were set to 250, 380, and 530 mm from the surface of the molten metal. Post-combustion analysis showed that the lowest gas velocity was observed under the condition of the highest nozzle height of 530 mm, and the high temperature and reaction zones were widely distributed in the lower region. Therefore, to facilitate heat compensation to the molten metal, it is necessary to control the gas velocity of the molten steelgas interface slowly.
1. 서 론
세계적으로 CO2 배출량 저감을 위해 신기후체제인 파리협정(Paris Agreement)이 2021년부터 발효됐으며 국내의 경우 2030년까지 2018년 CO2 배출량 대비 약 40%의 감축을 목표로 설정했다[1]. 국내 산업에서의 CO2 배출량을 비교해보면 철강분야는 38.3%의 수치로 CO2 배출이 높은 산업 중 하나로서 CO2 저감 방안이 시급한 실정이다[2-3]. 철강 제조 공정 중의 하나인 전로 제강에서는 CO2 저감을 위해 고철 사용량을 증대시켜 용선비를 감축시키는 방법이 있다. 그러나 전로 제강에서는 용선의 현열과 산화 반응열을 열원으로 사용하기 때문에 용선비를 감축할 시 용선의 현열 감소, 장입 고철에 의한 열 감소, 산화열 발생량 저감 등의 열 부족 문제를 야기하며 용강 온도 조절에 어려움이 생기게 된다. 따라서 온도 유지를 위해 열을 보상할 수 있는 기술인 2차 연소 기술(Post- Combustion Technology)에 대한 연구가 진행되어 왔다[4-6].
전로 내 2차 연소는 용강 내 C의 1차 연소로 CO 가스가 생성되고, 상부 랜스에 부착된 초음속 노즐을 통해 취입되는 산소 가스에 의해 CO가스가 연소되어 CO2 가스가 생성되는 반응이다. 2차 연소는 산소 가스가 분사되는 노즐의 위치 및 형상, 가스 유량, 수소 가스 유무 및 추가적인 2차 연소용 랜스에 의해 영향을 받는다고 알려지고 있다[7-9]. 효과적인 2차 연소 기술 개발을 위해서는 실제 설비에서 영향 인자 변화에 따른 2차 연소 거동을 규명하는 것이 필요하지만 공정 특성상 전로 내 가스 유동 영역에서의 가스 조성 측정이 용이하지 않으며 내부 상황을 가시적으로 확인하기가 어려운 문제가 있다. 또한 2차 연소 기술은 연소 반응이 발생하는 화학적 반응 뿐만 아니라 상부 랜스를 통해 취입되는 산소 가스의 분출과 주변 가스와의 혼합 거동도 매우 중요하게 다뤄진다. 이로 인해 수치적 방법을 이용하여 전로 공정에서의 가스 취입 및 2차 연소 반응에 대해 세계적으로 많은 연구가 수행되고 있다. Alam 등 [10]은 분위기 온도 조건을 상온에서 고온까지 변화시켜가며2차원의 단공(single hole) 노즐을 이용하여 초음속 제트 거동을 연구했고 특히 분위기 온도에 따른 중심축에서의 분출 가스의 속도 변화 및 온도 변화를 비교, 분석했으며, Kwon 등[11]은 초음속 노즐을 통한 가스의 분출 거동을 보다 상세히 연구하기 위해 단공 노즐 출구의 직경비를 1.0-2.0으로 변화시켜가며 2D 해석을 수행했다. Wang 등 [12]은 다공(multi hole) 노즐로부터 취입된 가스에 의한 제트 거동을 규명하기 위해 고온 분위기에서 4공 초음속 노즐의 각도에 따른 해석을 수행했고, Liu 등[13]은 5공 초음속 노즐에 부가적으로 중심축 노즐과 2차 연소용 노즐 여부에 따른 가스 제트 거동 연구를 통해 각 형상 별 속도와 압력 분포를 분석했다. 또한, 전로 상부 랜스를 통해 취입된 초음속 제트가 용강 및 슬래그 계면에 충돌하여 형성되는 캐비티(cavity) 형상을 규명하기 위해 수치적 해석 연구가 다수 진행되었다[14-16]. 그러나 2차 연소 거동 연구에 대해서는 대부분 단순 노즐 형상에서 산소 가스가 아음속으로 취입되었을 때의 연소 반응을 수행했으며[15,17-19], 초음속 노즐로 취입되었을 때의 연소 반응 연구는 매우 미흡한 실정이다. 전로 조업에서 상부 랜스에 부착된 노즐은 초음속 거동을 보이는 드 라발 (De Laval) 노즐을 사용하며, 드 라발 노즐을 통해 산소 가스가 취입될 때 노즐 출구에서 분출되는 가스는 압축과 팽창을 반복하며 초음속 제트가 형성되기 때문에 초음속 노즐과 아음속 노즐의 분출 거동은 현저히 다르게 나타난다. 가스의 유동이 달라지기 때문에 2차 연소 거동에도 영향을 미치며 실제 현상을 규명하기 위해서는 초음속 해석과 연소 반응을 같이 풀어야 할 필요가 있다. 따라서 본 연구에서는 전로 모사 가스 반응로와 초음속 노즐을 설계 및 제작하여 CO 가스 연소에 대한 기초 실험을 수행하고 수치해석 결과와 비교 분석하였다. 수치적 계산은 상용 유동 해석 프로그램인 ANSYS FLUENT를 사용하여 2차 연소 반응에 따른 가스 속도, 열 및 화학 조성 분포 특성을 확인했다. 2차 연소에 영향을 주는 인자 중 산소 가스가 분사되는 노즐의 높이를 변수로 정하였으며, 가스 반응로 형상, 노즐의 입구(inlet), 출구(exit) 및 노즐목(throat) 직경은 고정했다.
2. 이론적 배경
2.1 전로 내 화학 반응
제강 공정은 강 중의 불순성분을 제거하여 고청정, 고순도로 가는 과정에서 복잡한 화학 반응이 연쇄적으로 발생한다. 그 중 전로 공정을 보면 화학 반응은 그림 1과 같이 발생 위치에 따라 크게 용강-가스 제트 계면, 용강-슬래그 계면, 슬래그 형성, CO 연소 반응으로 나눌 수 있다[9]. 먼저 용강-가스 제트 계면은 상부 랜스를 통해 취입되는 산소 제트가 용강 및 슬래그와 충돌하여 캐비티를 형성하며 용강으로 침투하기 때문에 이 계면을 통해서 산화 반응이 일어나며 C, Si, P 등이 제거된다.
용강-가스 제트 계면 반응
슬래그-용강 계면에서는 P와 Mn에 의한 Fe 환원 반응이 일어나며 슬래그 형성을 목적으로 장입한 부원료에 의해 슬래그가 형성되고 밀도차로 인해 용강 위로 슬래그 층이 존재하게 된다.
용강-슬래그 계면 반응
슬래그 형성 반응
CO 연소 반응은 서론에서 언급한 바와 같이 탈탄 반응으로 생성된 CO 가스가 산소에 의해 연소되는 것을 말한다. 전로 배가스 내에는 많은 CO 함량과 열을 가지고 있으며 CO 가스가 연소될 때 C의 연소보다 2배 이상의 열량이 발생하기 때문에 추가 에너지 공급이 없는 전로 공정에서 좋은 연료로 사용될 수 있는 이점이 있다. CO 가스 연소의 평가는 식 11과 같이 가스 조성중 CO, CO2 분율의 비로 계산할 수 있으며 이를 2차 연소율(Post Combustion Ratio, PCR)이라 한다.
CO 연소 반응 (2차 연소 반응)
2.2 유동장 계산 이론
초음속 노즐을 통한 가스 거동 계산은 점성 유체의 유동과 압축성 유동에 대해 풀이가 가능한 Navier-Stokes 방정식을 지배방정식으로 사용할 수 있다. 정상상태에서의 질량, 운동량 및 에너지 보존 방정식은 다음과 같다 [20].
Mass conservation equation
여기서 ρ는 기체의 밀도(kg/m3), ui는 i 방향의 속도 (m/s), xi는 i 방향에 대한 공간좌표를 나타낸다.
Momentum conservation equation
여기서, p는 기체의 압력(Pa), μ는 기체의 점도(kg/m·s)를 나타낸다.
여기서, E는 총 에너지(J/kg), Jj는 화학종 j의 확산플럭스(kg/m2), T는 기체의 온도(K), keff와 μeff는 각각 유효 열전도율(W/m·K)과 유효 점도(kg/m·s)를 나타낸다. hj항은 화학종 j의 현열엔탈피(J/kg)로 다음과 같이 표현된다.
여기서 Cp는 비열용량(J/K)을 의미한다.
본 연구에서는 standard k-ε 모델에 비해 우수한 예측성을 보인다고 알려진 realizable k-ε 모델을 사용하여 해석을 진행했다. 이 모델의 난류 에너지(k, J/kg)와 에너지 소산율(ε, J/kg·s)은 다음의 방정식으로 표현된다.
난류 운동에너지 방정식
에너지 소산율 방정식
여기서 난류 점도는 다음과 같다.
Cμ는 standard k-ε 모델에서 실험적인 상수로 사용되었지만 realizable k-ε 모델에서는 다음과 같이 표현된다.
두 개 이상의 혼합된 물질의 유동 계산에 사용되는 species transport 모델을 선택하여 화학종 계산을 진행했다. 이 모델은 대류-확산 방정식의 해를 통해 각 화학종의 질량 분율을 예측하며 보존 방정식은 다음과 같다.
여기서 Yi는 화학종 i의 질량 분율, Ri는 반응에 의한 화학종 i의 생성 속도, Si는 분산상과 소스 항에 의한 생성 속도를 의미한다. 층류와 난류 유동의 확산플럭스는 다르게 표현되는데 본 연구에서 고려한 난류 유동에서의 확산플럭스 J는 다음과 같다.
여기서 Di,m은 혼합물에서 화학종 i의 확산계수(m2/s), Sct는 난류 슈미트 수, DT,i는 열확산계수를 나타낸다.
2.3 반응 계산 이론
전로 내 2차 연소 중 일어나는 화학 반응은 반응 속도에 대한 정보가 제한되어 있으며, 반응이 일어나는 영역은 난류영역으로 난류에 의한 영향도 고려해야 되기 때문에 많은 연구들에서 비교적 단순하고 난류 연소현상을 잘 모사할 수 있는 해석 방법 중의 하나로 난류에 의한 혼합이 율속 단계라는 가정하에 연소 반응을 모사해왔다. Eddy dissipation 모델로 알려진 난류-화학 상호작용 모델은 다음과 같이 표현된다.
여기서
3. 실험 및 해석 방법
3.1 실험 조건
CO 연소 시험 장치는 130 kg 규모 전로에서 용융상 위의 가스 유동 영역을 가정하여 노구 직경 200 mm, 노저 직경 500 mm, 높이 632 mm의 치수로 전로 내 가스 반응이 일어나는 가스 유동 영역을 제작했다. CO 가스 연소 반응의 기초 연구로서 슬래그의 형성과 가스에 의한 용강 표면 형상 변화는 고려하지 않았기 때문에 반응로 하부는 캐비티가 없이 평평하게 설정했으며, 반응로 외측은 분리 및 조립이 용이한 철피, 내측은 부정형 내화물로 구성되어 있다. 상부 랜스는 내경 20 mm이며 노즐 입구부터 노즐목까지 단면적이 작아지는 형태(converging)로 랜스 끝단에 부착된 초음속 노즐은 노즐목 1.9 mm, 노즐 출구 1.9 mm로 노즐목에 대한 노즐 출구의 직경비(De/Dt) 1.0으로 부족 팽창(under expansion) 거동을 보이는 노즐을 채택했다. 실험장치는 그림 2의 모식도와 같다. 산소 가스 취입량을 산정하기 위해 취련 시간은 20분으로 가정하고 용선량, 탄소 함량 및 취련 시간을 통해 모사 장치에서의 이론 탈탄량을 계산하였다. 계산한 이론 탈탄량을 통해 CO 가스 발생량을 계산하면 약 547 L/min을 얻을 수 있다. 이때, 50%의 PCR을 갖도록 산소 가스 취입량을 도출했다. 실험 시에는 PCR 100%의 완전 연소 반응이 일어날 수 있도록 CO 가스량을 조정하여 상부 랜스와 끝단에 부착된 초음속 노즐을 통해서 산소 가스를 150 L/min으로 취입하고 용강 표면에서의 CO 가스 발생을 묘사하기위해 반응로 바닥에 매설된 포러스 플러그(porous plug)를 통해서 CO 가스를 300 L/min으로 취입했다. 전로 제강에서는 상부 랜스 높이에 따라 조업 특성이 달라지기 때문에 랜스 높이가 CO 연소 반응 거동에 미치는 영향을 비교하기 위해 탈부착이 가능한 노즐의 출구가 반응로에 위치하는 높이(H)를 용강 표면으로부터 각각 250, 380, 530 mm가 되도록 변경하여 실험을 수행했다. 실험 중에 변화하는 온도 및 2차 연소율을 측정하기 위해 3개의 열전대(Thermocouple, T/C)를 용강 표면으로부터 각각 100, 250, 450 mm 떨어진 지점의 벽면에 매설하고 랜스 상단에 가스 분석기(MRU, MGA5 plus)를 부착하여 배가스 내 O2, CO, CO2 가스 농도를 분석했다. 가스 취입 전 내화물을 예열하여 100 mm 높이의 T/C(T/C1)에서 1523.15 K이 유지됨을 확인하고 가스 분석 및 산소, CO 가스 공급을 차례로 실시하여 120초 동안 반응을 진행했다. 가스 개시 120초 후 CO, 산소 가스의 공급을 차단하고 가스분석을 중단하였다.
3.2. 해석 조건
상부 랜스를 통해 취입되는 산소 가스와 하부에서 취입되는 CO 가스의 연소 반응에 의한 노내 가스 거동을 해석하기 위해 벽면두께 없이 가스 유동영역 형상만 작성하여 2차원 축대칭 조건을 설정하고, 해석 영역의 격자는 사각(quadrangle) 형태로 작성하여 약 150,000개의 격자로 분할했다. 특히 노즐부는 전체 형상에 비해 상대적으로 치수가 매우 작고 상세한 해석이 필요하므로 격자 크기를 출구부의 격자 크기 대비 최소 1/10을 적용하여 세밀하게 작성했다. 계산에 사용된 해석 형상은 그림 3에 나타냈으며 상세 치수는 표 2와 같다. 정상상태에서의 유동장 내 가스 속도, 온도 및 화학 조성 데이터를 얻기 위해 2.2, 2.3 절에 정리한 realizable k-ε 모델 및 eddy-dissipation 모델을 적용하고, SIMPLE algorithm으로 반응을 계산했다. 초기 유동장 온도는 실험과 동일하게 1523.15 K으로 설정하고, 취입 가스의 경우 산소 가스는 300.00 K으로 취입, CO 가스는 포러스 플러그를 통과하며 예열 된 후 가스 반응로 내로 취입되기 때문에 이를 고려하여 1523.15 K으로 입력하여 계산을 수행했다. 화학 반응은 CO 가스가 산소 가스에 의해 연소되어 CO2 가스가 생성되는 비가역 반응만을 고려하였으며 실험과 동일하게 산소와 CO 가스 유량을 각각 150과 300 L/min으로 취입하여 완전 연소될 수 있게 설정했다.
4. 결과 및 고찰
4.1 노즐 높이에 따른 가스 유동 해석
노즐 출구에서 산소 가스의 분출 거동은 노즐 출구부와 목부의 비(De/Dt)가 동일한 형상의 노즐을 사용했기 때문에 모두 같은 양상을 보이며 그림 4에 노즐 높이별 중심축에서의 속도변화를 나타냈다. 높이별 중심축에서의 노즐 출구 직후 속도 변화를 보면 출구에서 가장 빠른 속도를 보이며 노즐 팁에서 멀어질수록 속도가 감소한다. 출구 직후 속도는 약 460 m/s로 마하수(mach number)로 환산하면 약 1.35를 얻을 수 있고, 설계 노즐을 통과하여 분출되는 가스가 초음속 거동을 보임을 알 수 있다. 이때 출구 직후 일정 구간동안 속도가 유지되는 것을 볼 수 있는데, 이를 포텐셜 코어(potential core)라 한다. 그림 5는 노즐 출구에서 가스 분출거동을 확인하기 위해 H380 조건일 때 노즐 출구에서의 가스 속도와 압력을 나타냈다. 그림 5(a)에서 출구 직후 분출된 가스는 팽창과 수축을 반복하는 것을 확인할 수 있고 이는 분출 가스와 대기와의 압력차이로 인해 발생하게 된다. 속도와 압력 거동을 비교해보면 출구 직후 가스 압력이 대기보다 크기 때문에 초기에는 부족 팽창(under expansion) 거동이 일어난다. 이후 Point 1에서 가스 압력이 대기보다 작은 것을 볼 수 있으며 다시 가스 압력이 대기보다 커지게 되는 Point 2에 도달할 때까지 가스는 수축함을 보이고 있다. 팽창과 수축이 반복되는 포텐셜 코어 구간 이후에는 그림 4에서와 같이 에너지 손실로 인해 가스 속도가 급격히 감소하게 된다. 본 해석에서는 노즐 치수가 매우 작고 전로 조업 시 취입하는 압력보다 작게 취입했기 때문에 통상적으로 유지되는 포텐셜 코어 길이 보다 짧게 나타난 것을 확인했다[11]. 노즐 높이에 따른 내부의 유속을 비교해보기 위해 속도 범위를 0 – 50 m/s로 변경하여 속력 및 유동 분포를 그림 6에 나타냈다. 반응로 내부 가스 유동은 노즐 높이에 따라 서로 상이한 결과를 보이고 있다. 용강 표면에서 노즐 출구까지 거리가 가장 짧은 H250 조건의 경우 랜스가 노 내로 깊이 들어와 있어 탕면을 빠른 속도로 이동한 후 벽을 따라 상승하여 1차 순환 유동이 크게 형성된다. 다만 노 벽을 따라 빠른 속도로 상승한 것과 달리 중심축으로 순환하는 동안은 유속이 느려짐을 확인할 수 있다. H380 조건에서는 노즐 출구가 H250 조건보다 높은 위치에 있기 때문에 하부에 도달하는 가스 속도가 감소하여 용강 표면 부근에서 1차 순환 유동이 형성되며 중심축으로 순환할 때도 높은 유속을 보이고 있다. 반대로 H530 조건에서는 H380 조건보다 1차 순환 유동의 크기가 크고 높게 나타남을 볼 수 있다. 이 경우에는 H250과 H380 조건에서 용강 표면에 충돌하는 가스속도 차이로 인한 1차 순환 유동에 높이차가 발생하는 현상과 다르게 상승기류로 인해 넓은 영역의 1차 순환 유동이 형성되고 바닥 및 내부에서 다른 조건들보다 상대적으로 느린 유속을 보인다. 2차 순환 유동은 1차 순환 유동의 위치와 크기에 따라 형성되는 위치와 크기가 달라지게 된다.
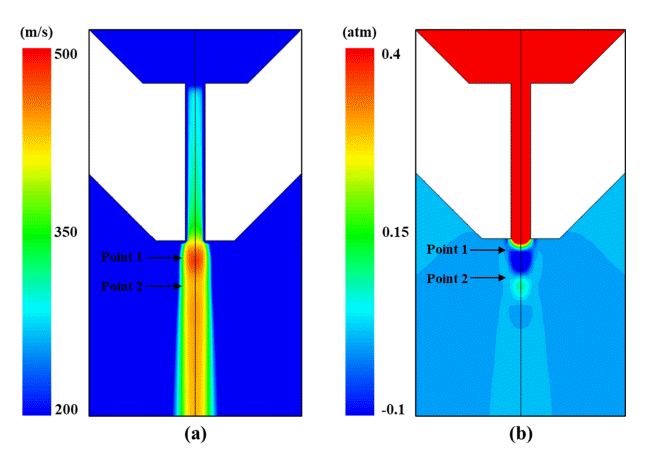
Calculated results of gas velocity and static pressure distribution for H380. (a) velocity, (b) static pressure.
4.2 노즐 높이에 따른 온도 분포 해석
그림 7은 용강 표면에서 노즐까지의 거리를 250, 380, 530mm로 변화시켰을 때, 각각의 조건에서 형성되는 반응에 따른 노내 온도 분포를 보여준다. 노즐 출구 직후에서는 초음속 가스거동에 의해 온도가 가장 낮고, 제트 부근에서 빠르게 반응이 일어나 온도가 급격히 상승하기 때문에 출구에서 멀어질수록 온도가 상승한다. 이 후, 빠르게 분출되며 반응에 참여하지 못한 가스가 고온의 가스와 같이 순환 유동을 하기 때문에 이 영역에서 추가적인 연소 반응이 발생하며 점점 온도가 상승한다. D와 E는 각각의 조건에서 반응이 완료된 고온의 가스가 상승 유동을 하며 노구를 통해 배출되는 구간이다. 또한 노즐 높이가 높아질수록, 즉 용강 표면에서 멀어질수록 고온 영역의 범위가 넓게 퍼짐으로써 연소 반응이 넓은 영역에서 일어난다고 판단된다. 반응 영역 확인을 위해 그림 8에 각 조건에 대한 반응열 분포를 나타냈다. 유동 양상에 따라 반응 영역이 형성되는 구간에 차이가 발생하는데, 1차 순환 유동이 크게 형성되는 H250, H530 조건에서 반응 영역도 경사벽 부 아래까지 높게 나타난다. 다만 하부 유속이 느린 H530 조건에서 보다 두껍게 나타나며 반응 영역이 더 넓음을 알 수 있다. H380은 1차 순환 유동 영역과 동일하게 벽 부 중앙까지 반응 영역이 형성되고 H250 보다 영역의 두께가 좁아지는데 이는 1차 순환 유동 영역이 보다 작게 형성되어 중심축으로 순환하는 가스 속도가 더 높기 때문이다.
온도에 대한 실험과 해석 결과를 비교 분석하기 위해 벽 부 T/C가 매설된 위치에서의 실험 전후 온도를 추출하여 승온량을 비교하였다. 그림 9을 보면 해석시의 승온량이 모든 조건에서 높게 나타나며, 이는 120s에서의 실험 결과와 정상상태에서의 해석 결과를 비교했기 때문에 나타난 결과로 사료된다. 다음으로 노즐 높이 별 온도 변화를 보면 실험과 해석 모두 노즐 높이 상승 시 상단의 경사 벽 부에 위치한 T/C3의 온도는 지속적으로 상승하며 탕면에 가깝게 위치한 T/C1은 H380 조건에서 약간 하락 후 H530에서 크게 상승하는 것을 알 수 있다. 하지만 T/C2의 온도는 서로 다른 거동을 보이는데 실험에서는 T/C1에서의 승온량과 미미한 차이를 보이고 있지만 해석에서는 T/C3의 승온량과 유사하게 나타난다. T/C1과 3을 통해 실험과 해석 결과의 절대적인 승온량은 다르지만 온도의 하락 상승 경향은 유사하게 나타남을 확인했으며, T/C2에서 상이한 결과가 나온 것은 실험보다 해석을 통한 연소 반응이 보다 빨리 진행된 것으로 보인다. Naito 등[19]의 연구에서도 실험보다 해석에서 상대적으로 반응이 빠르게 진행된 것을 볼 수 있으며, 이는 반응의 율속 단계를 난류에 의한 혼합으로 가정하여 나타난 결과로 보고되고 있다. 노즐 높이 변화에 따른 속도 및 열 분포 해석 결과 양상이 유사하다는 점을 통해 실험에서는 가시적으로 확인하지 못한 속도 유동이 해석 결과와 근접할 것이라고 생각된다. 또한 3개의 조건들 중 상대적으로 내부 유속이 느린 H530 조건일때 탕면 부근에서 높은 온도를 보이며, 내부 유속이 가장 빠른 H380 조건에서 보다 높은 온도가 나타나는 것으로 보아 2차 연소 반응은 내부 가스의 속도에 영향을 받는다고 판단되며 일반적으로 2차 연소를 촉진하기 위해 산소 속도를 감소시켜야 한다는 연구[21]와 상응하는 결과로 확인했다.

Comparison between experiment and numerical analysis of temperature change before and after the reaction at the T/C location.
반응 후 노구로 배출되는 가스의 흐름을 보다 상세히 알아보기 위해 노구를 0 mm로 놓고 아래로 100 mm 높이마다 최대 온도의 위치를 추출하여 그림 10에 나타냈다. 데이터 점을 연결한 경로가 완전히 일치하지는 않지만 3가지 조건 모두 용강 표면에서 벽 부로 이동한 후 경사 벽 부 영역을 타고 이동하는 것을 볼 수 있다. H250은 500 mm 높이일 때 벽 부가 아닌 제트 부근에서 최대 온도점을 보이는데 이는 다른 조건들 보다 산소 가스가 더 빠른 속도로 탕면에 충돌한 후 벽 부로 이동하므로 벽 부에서는 상대적으로 온도가 낮기 때문이다.
4.3 노즐 높이에 따른 가스 조성 분포 해석
계산이 완료된 후 평형상태에서의 반응로 내 O2 , CO, CO2 가스 조성 분포를 그림 11에 나타냈다. 먼저 그림 10(a)에 중심축에서의 화학종 분포를 보면 모든 조건에서 산소와 CO2 분포를 통해 산소 가스가 초음속 노즐에서 분사된 직후부터 연소 반응이 발생해 산소 가스가 소모되고 CO2 가스 생성이 확인되며 두 화학종은 서로 반비례 양상을 보인다. 다만 노즐 높이별로 용강 표면에 도달하는 속도가 달라짐에 따라 산소 가스 분율에 차이를 보이고 있다. H530 조건은 하부에서 가장 느린 유속으로 CO 연소 반응이 활발히 발생하여 산소 분율이 가장 낮음을 알 수 있다. 다음으로 H380 조건에서의 반응로 내부 가스 분포를 나타낸 그림 10(b)을 보면 산소와 CO 가스는 연소 반응물로 사용되기 때문에 반응로 내에서 분율이 적게 나타나고 CO2 가스는 반응 생성물로서 반응로 내부에서 높은 분율을 차지한다. CO 가스는 하부에서 취입 직후 바로 연소 반응에 의해 소모되어 산소 제트와 바로 접촉하는 중심부에는 존재하지 않고 가스 흐름에 따라 벽 부 쪽으로 밀려나 매우 적은 양의 미반응 가스가 존재하는 것을 확인했다. 계산이 완료된 후 반응로 외부로 빠져나가는 배출가스의 CO, CO2 가스 분율로 PCR을 계산하기위해 노구 위치에서 O2 , CO, CO2 가스 조성을 추출 후 그 데이터와 PCR 계산값을 표 3에 나타냈다. 3절에 서술한 바와 PCR 100%가 되도록 산소와 CO 가스의 취입량을 조절해주었기 때문에 표 3과 같은 결과를 얻을 수 있었다. 실험과 해석의 가스 조성 변화 및 PCR을 비교하기 위해 H380 조건의 가스 조성 결과를 그림 12에 나타냈다. 해석과 마찬가지로 PCR은 100%를 보이는 것을 확인했으며, 산소 가스 조성의 경우 실험이 종료될 때까지 약 5%의 분율을 보이고 있다. CO 가스의 분율이 0%이기 때문에 취입된 산소와 CO 가스가 완전 연소함을 알 수 있고 따라서 산소 가스 분율의 경우 미 반응된 양이 아닌 외기에 의한 분율로 확인했다.

Profile of O2, CO and CO2 mass fraction for nozzle height from numerical analysis. (a) mass fraction of gas along the center axis for nozzle height, (b) distribution of mass fraction under H380.
5. 결 론
전로 조업에서 효율적인 2차연소 기술에 대한 기초 연구를 수행하기 위해 단공 노즐을 부착한 상부 노즐 높이에 따른 실험과 수치해석을 진행했으며 용강으로의 열 보상 효과 및 노내 가스 거동을 비교하여 다음과 같은 결론을 얻었다.
노즐 높이에 따라 반응로 내 가스 거동이 서로 상이하게 나타나며 1차 순환 유동의 크기는 H530, H250, H380 순으로 크게 나타나며 H250은 내부로 깊게 들어온 상부 랜스에 의해 취입된 제트가 용강 표면을 빠른 속도로 이동 후 벽을 타고 상승하여 큰 순환 유동이 형성되고 H530의 경우 가스 속도에 의한 것이 아닌 상승기류에 의해 넓은 순환 유동이 형성되어 다른 조건들 보다 느린 유속을 보인다.
내부 온도 분포는 가스 속도 분포와 유사한 양상을 보이며 반응로 하부는 H530, H250, H380 순으로 고온을 보인다. H250과 H530은 모두 1차 순환 유동이 크게 형성되는 조건으로 반응 영역의 위치는 경사 벽 부 아래까지 동일하게 나타나지만 영역의 크기는 가스 속도가 낮은 H530에서 보다 넓게 형성된다. H380은 H250 보다 산소 제트가 하부에 도달하는 속도가 느리지만 중심축으로 순환하는 내부 가스 속도는 더 빠르기 때문에 반응 영역이 더 작게 형성됨을 확인했다. 따라서 유속에 따라 반응 영역과 온도가 결정되며 효과적인 2차 연소 기술을 위해서는 하부 유속을 느리게 제어해야 할 것으로 사료된다.
실험 및 해석이 종료된 후 각각의 T/C 위치에서 승온량을 비교한 결과T/C1과 3이 위치한 하부와 상부는 절대적인 온도변화의 차이는 있지만 변화하는 경향성은 유사한 것을 확인했다. 하지만 T/C2가 위치한 중앙부에서는 상이한 거동을 보이는데 이는 실험보다 해석시에 반응이 하부에서 빨리 종료되기 때문에 상부에 위치한 T/C3과 유사한 승온량이 나타난 것으로 판단된다. 따라서 반응로 중앙부에서의 반응 속도 제어를 위해 연소 해석 모델의 추가 검토가 필요할 것으로 판단된다.
화학종 분포를 통해 연소 반응은 즉각적으로 일어남을 알 수 있고, 노구에서의 CO와 CO 2 분율을 통해 PCR을 계산한 결과 100%를 얻어 취입한 가스들이 완전연소 함을 확인했다. 다만 실제 전로 조업에서는 PCR 수치가 100%가 아니기 때문에 산소와 CO 가스의 취입비 변화에 따른 2차 연소 반응 거동에 대한 후속 연구가 필요하다고 사료된다.
Acknowledgements
본 연구는 산업통상자원부 (MOTIE)와 한국에너지기술평가원 (KETEP)의 지원 (No. 20172010106310) 과 인하대학교의 지원에 의해 연구되었으며, 이에 감사드립니다.